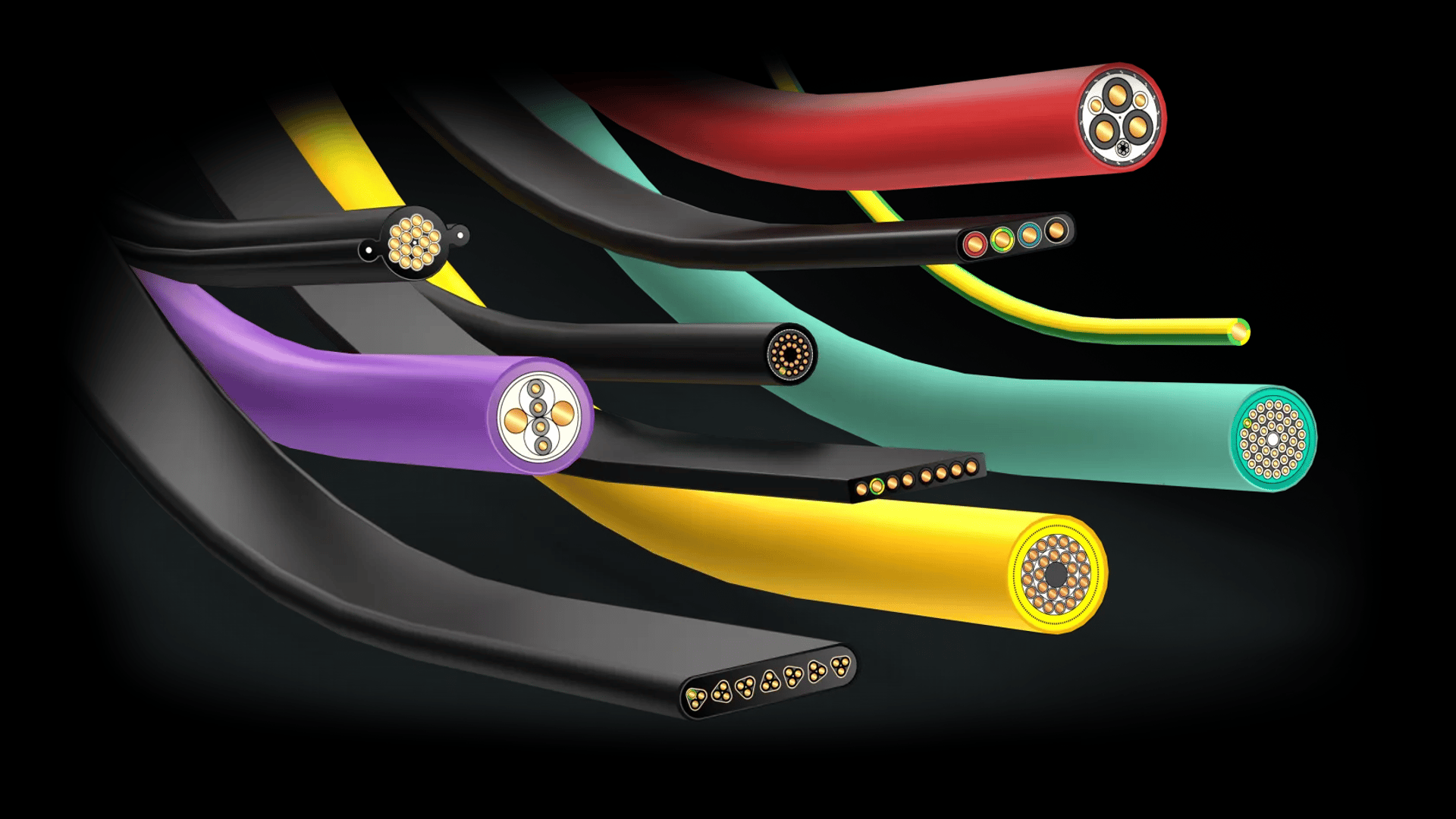
Suitable for any energy supply on cable drums and festoon systems associated with high mechanical stresses, frequent bending/torsion operations and fast movements with strong accelerations.
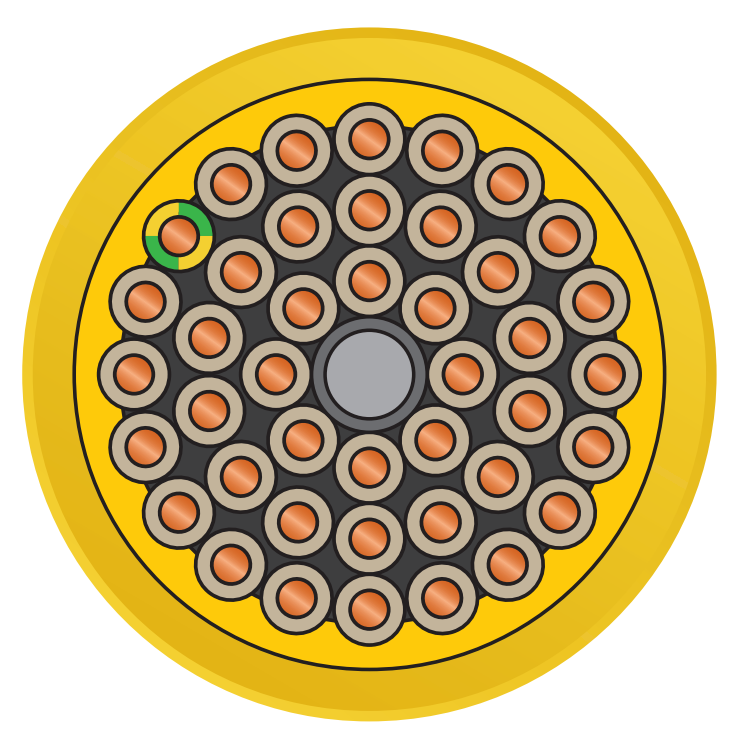
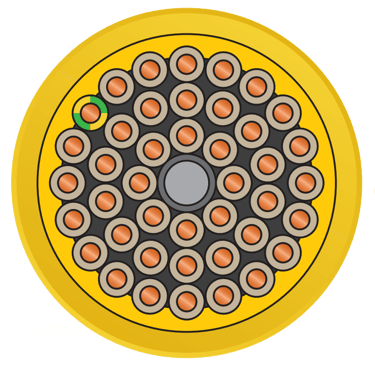
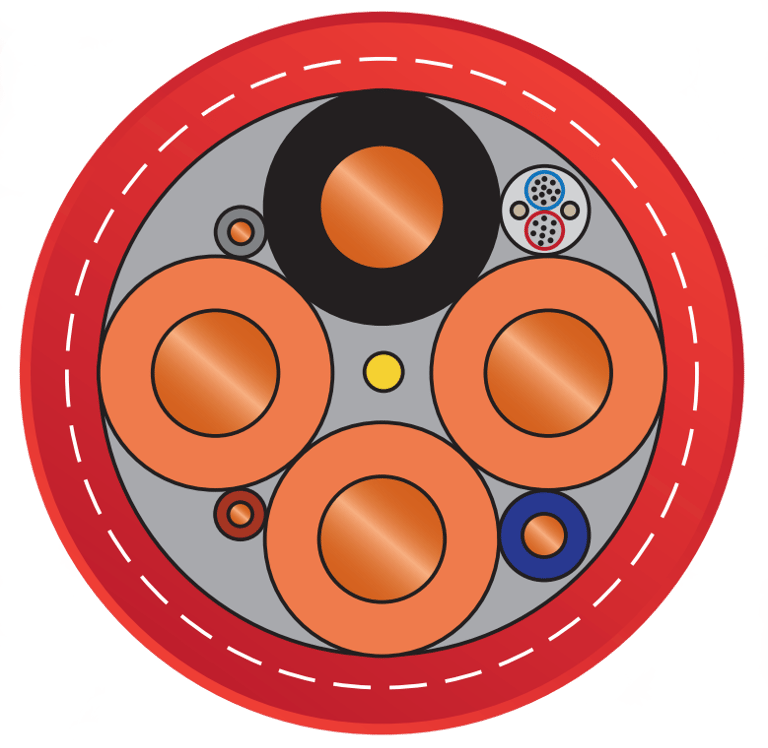
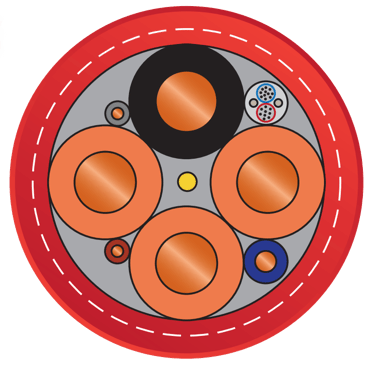
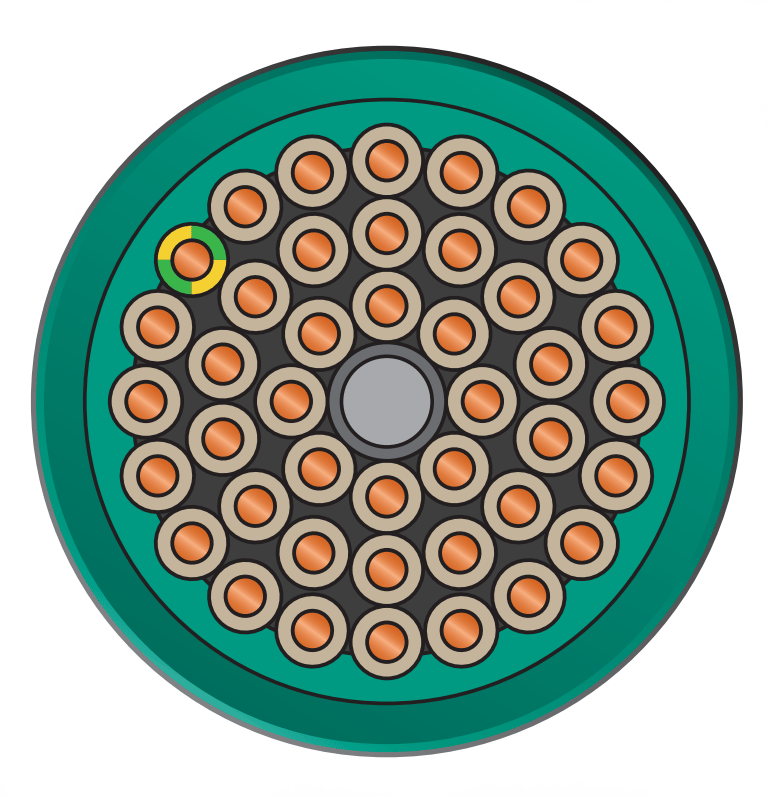
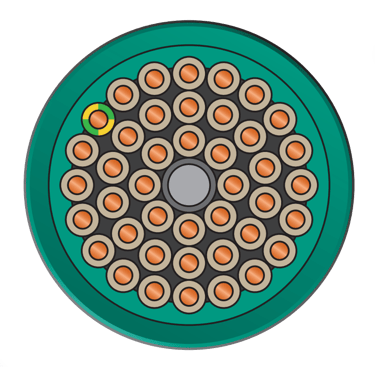
Our factory is a testament to our unwavering commitment to high standards and exacting requirements, setting a new benchmark in the Cable industry.
Step into our facility, and you'll find an array of cutting-edge machinery that forms the backbone of our operations. Automated production lines seamlessly weave together precision and efficiency, ensuring that every cable crafted is a masterpiece of modern technology.
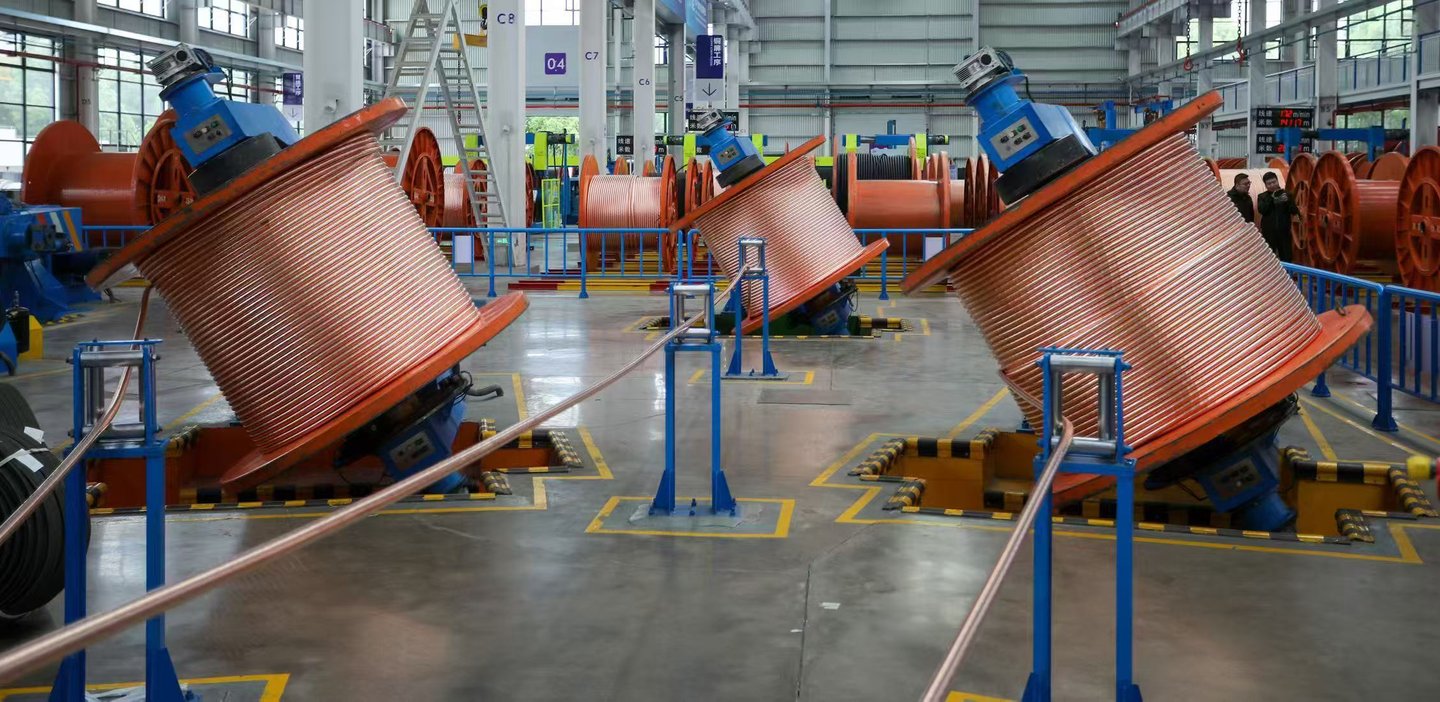
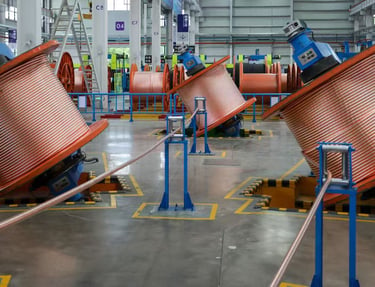
Cutting-Edge Machinery:
Stringent Quality Control:
Our factory operates with a meticulous eye for detail, implementing stringent quality control measures at every stage. From the initial inspection of raw materials to the final testing of finished products, our commitment to excellence ensures Feichun stands as a symbol of reliability.
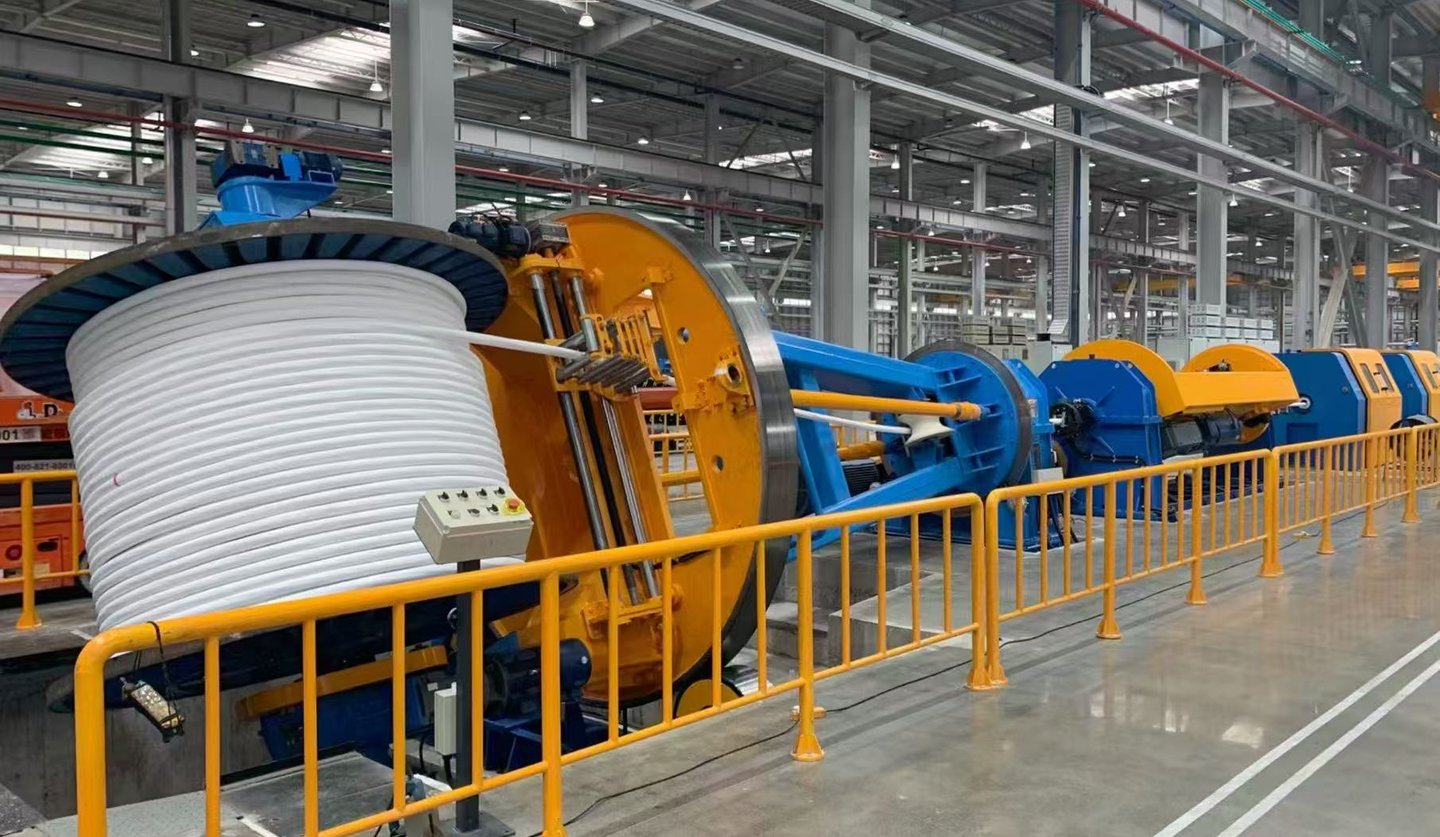
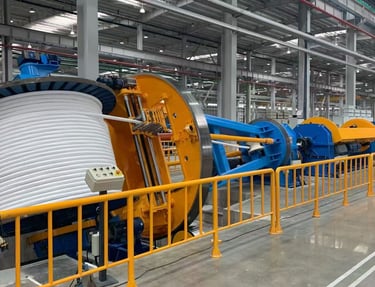
Our distinguished Research and Development (R&D) department stands as the pulsating heart of groundbreaking cable technology.
Our R&D department comprises a cadre of seasoned engineers and scientists, a powerhouse dedicated to propelling cutting-edge cable technology. Their collective expertise ensures that we consistently lead the industry with innovative solutions.
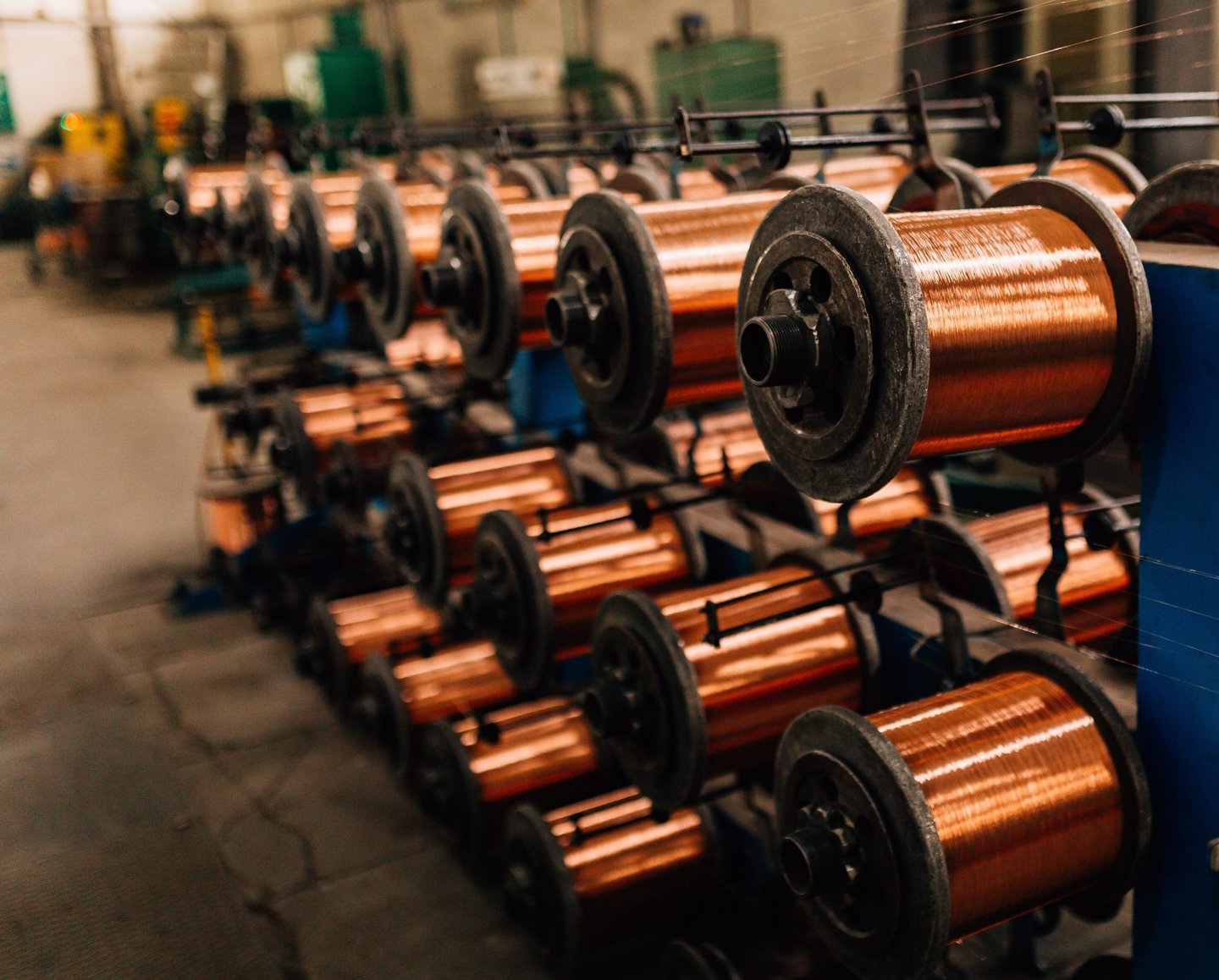
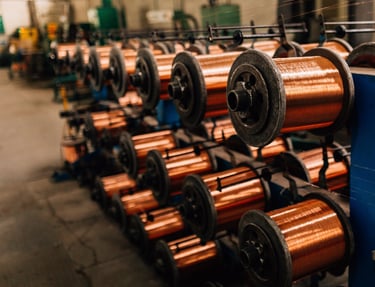
Exceptional Team:
Tailored Design and Development:
With a focus on innovation and customization, we embark on a journey of tailored design and development. Whether it's OEM manufacturing to match your exact specifications or ODM services for original product creation, our skilled engineers.
Understanding Reeling Cables for Mobile Machinery in Port Terminals and Shipyards
Reeling cables play a critical role in maritime infrastructure, serving as the backbone for mobile machinery in port terminals and shipyards. Designed to handle dynamic motion, harsh environmental conditions, and heavy mechanical stress, these cables are essential for ensuring reliable operations. This article explores the key challenges in reeling cable management and practical solutions to optimize their performance and lifespan.
1. Introduction to Reeling Cable Systems
1.1 Defining Reeling Cables
Reeling cables are specialized electrical cables engineered for continuous movement, often under extreme conditions. Unlike standard electrical cables, they are designed to endure repeated bending, coiling, and uncoiling without compromising performance.
In port and shipyard environments, reeling cables are vital for machinery such as cranes, mobile gantries, and automated guided vehicles (AGVs). Their unique features include:
High tensile strength to withstand constant pulling forces.
Resistance to environmental factors such as saltwater and UV radiation.
Advanced insulation and sheathing to prevent wear and electrical degradation.
1.2 Operational Environment Challenges
Reeling cables must endure extreme environmental conditions often encountered
in maritime operations, including:
Salt water exposure that accelerates corrosion and degrades cable materials.
Mechanical stress from constant movement and heavy loads.
Temperature variations from freezing cold to scorching heat.
Corrosive industrial atmospheres laden with chemicals and pollutants.
2. Technical Specifications and Design Considerations
2.1 Cable Construction
The construction of a reeling cable is meticulously designed to handle demanding conditions. Key components include:
Conductor materials: Typically made from stranded copper for flexibility and high conductivity.
Insulation types: Durable polymers such as cross-linked polyethylene (XLPE) or ethylene-propylene rubber (EPR).
Protective sheathing: Materials like polyurethane (PUR) or chlorinated polyethylene (CPE) provide resistance to abrasion, water, and chemicals.
Special engineering ensures cables can endure continuous flexing and movement without fatigue or failure.
2.2 Key Performance Parameters
Electrical characteristics:
Voltage ratings: Determining the operational power range.
Current carrying capacity: Ensuring safe and efficient power delivery.
Resistance and impedance: Maintaining signal integrity and minimizing energy loss.
Mechanical specifications:
Bend radius: Defines how tightly a cable can be coiled without damage.
Flex life expectancy: Measures durability under repetitive motion.
Load-bearing capabilities: Ensures cables can handle the physical strain of mobile machinery.
2.3 Material Selection
Reeling cables used in maritime settings rely on specialized compounds that provide:
UV resistance to withstand prolonged sun exposure.
Chemical resistance against oils, fuels, and industrial chemicals.
Mechanical abrasion resistance to prevent wear from constant movement.
Waterproofing to protect against saltwater intrusion.
3. Operational Challenges and Solutions
3.1 Common Failure Modes
Despite their robust design, reeling cables can fail due to:
Mechanical wear from repeated bending and stretching.
Electrical degradation caused by insulation breakdown or conductor damage.
Environmental damage from moisture, salt, and UV exposure.
Improper installation and maintenance, leading to premature failure.
3.2 Preventive Maintenance Strategies
To extend the life of reeling cables, adopt these preventive maintenance techniques:
Regular inspections to identify wear and damage early.
Proper cable routing to minimize stress during operation.
Lubrication and protective coatings to reduce friction and corrosion.
Employing predictive maintenance technologies, such as smart monitoring systems, to track cable performance and preempt failures.
4. Application-Specific Considerations
4.1 Mobile Machinery Types
Reeling cables are indispensable for various mobile machinery, including:
Container handling equipment: Ensuring seamless movement of goods.
Ship-to-shore cranes: Critical for loading and unloading vessels.
Mobile gantry systems: Used in shipyards for large-scale operations.
Automated guided vehicles (AGVs): Supporting autonomous operations in ports.
4.2 Cable Selection Criteria
Choosing the right reeling cable involves assessing:
Load requirements: Matching the cable’s capacity with machinery demands.
Movement patterns: Accounting for bending, twisting, and flexing.
Operational constraints: Factoring in environmental conditions and space limitations.
5. Safety and Compliance
5.1 Regulatory Standards
Reeling cables must meet stringent international maritime regulations, such as:
IEC 60228 for conductor specifications.
ISO 9001 for quality assurance.
Electrical safety standards like IEC 60332 for flame retardance.
5.2 Risk Mitigation
Effective risk mitigation strategies include:
Installing fault protection systems to prevent electrical hazards.
Ensuring proper mechanical support to avoid physical damage.
Training personnel on safe handling and operation of reeling cables.
6. Advanced Technologies and Innovations
6.1 Emerging Cable Technologies
Recent advancements in reeling cables include:
Smart monitoring systems: Detecting wear and performance issues in real time.
Self-healing materials: Automatically repairing minor damage.
Advanced composite technologies: Enhancing strength and flexibility.
Integrated diagnostic capabilities: Simplifying maintenance and troubleshooting.
6.2 Future Trends
The future of reeling cables lies in:
Automation: Adapting to the rise of autonomous port operations.
Sustainable materials: Reducing environmental impact.
Enhanced durability: Using next-generation polymers for extended lifespan.
7. Practical Troubleshooting Guide
7.1 Diagnostic Techniques
Effective troubleshooting involves:
Visual inspections: Identifying cracks, abrasions, or deformation.
Electrical testing: Measuring continuity, insulation resistance, and voltage drop.
Performance assessments: Checking for deviations in operational efficiency.
7.2 Common Problem Resolution
For common issues:
Replace cables showing significant wear.
Use emergency repair kits for temporary fixes.
Consult experts to decide when to repair or replace damaged cables.
8. Case Studies
8.1 Successful Implementation Scenarios
Real-world examples demonstrate:
Efficiency improvements with advanced cable designs.
Cost-saving strategies through predictive maintenance.
Technological breakthroughs in material science and cable monitoring.
8.2 Lessons Learned
Insights from the field:
The importance of regular maintenance.
Best practices for routing and protection.
Value of investing in high-quality cables.
9. Economic and Operational Impact
9.1 Cost-Benefit Analysis
Understanding the financial implications:
Higher initial investment for durable cables pays off in reduced downtime.
Long-term savings through minimized repair and replacement costs.
Enhanced productivity by ensuring uninterrupted operations.
9.2 Total Cost of Ownership
Factors influencing ownership costs:
Maintenance expenses: Regular upkeep reduces failures.
Downtime reduction: Reliable cables prevent operational delays.
Performance optimization: High-quality materials ensure efficiency.
Conclusion
Reeling cables are a strategic investment for port terminals and shipyards, ensuring reliable and efficient operations. By understanding their design, maintenance needs, and technological advancements, industry professionals can make informed decisions that optimize performance and reduce costs.
Appendices
Technical glossary: Definitions of key terms.
Detailed specification tables: Comparisons of cable types.
Manufacturer comparison chart: Features and benefits of leading brands.
Recommended selection guidelines: Tips for choosing the best cable.
References
International standards: IEC, ISO.
Technical publications and research papers.
Manufacturer documentation.
About the Author/Contributors
Our team of experts combines years of experience in maritime infrastructure and cable technology. With a commitment to innovation and quality, we provide insights that empower industry professionals to achieve their goals.
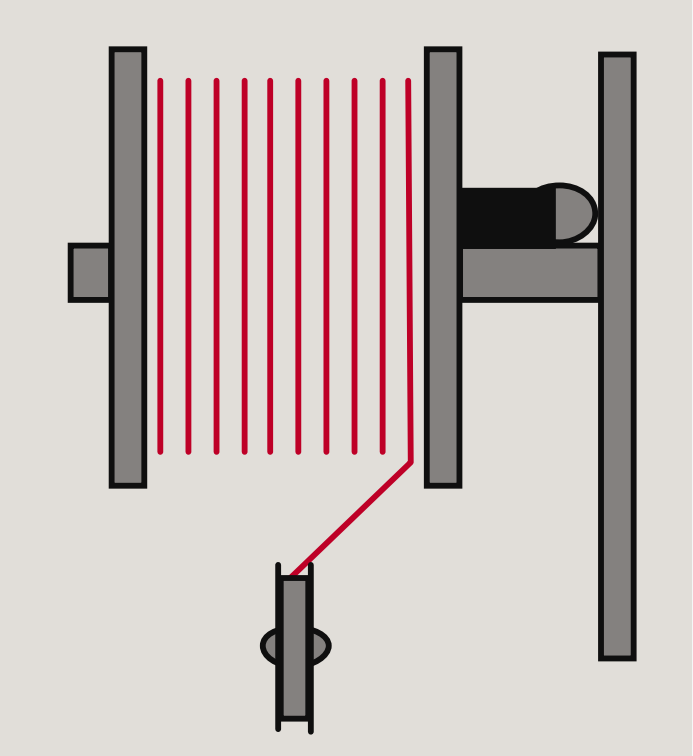
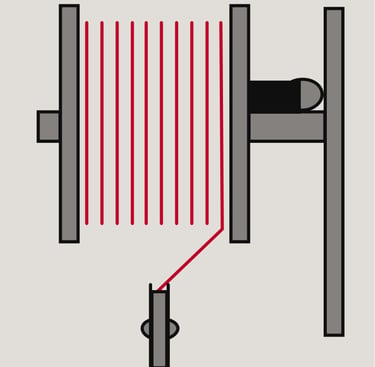
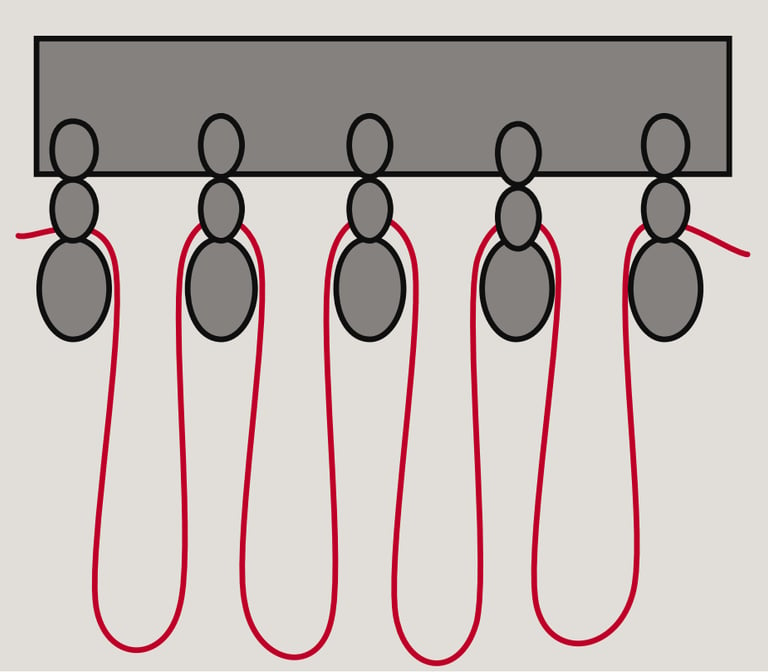
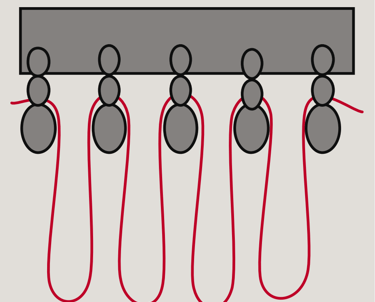
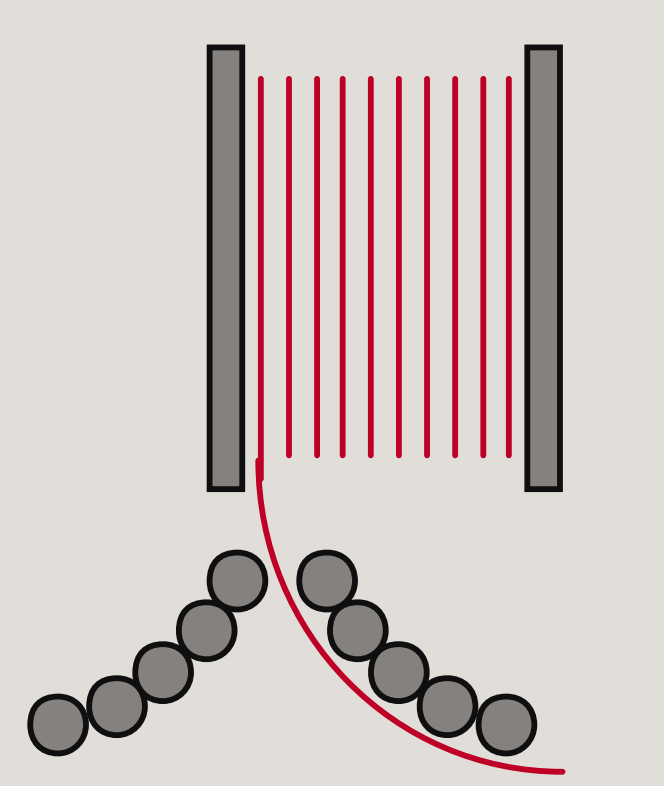
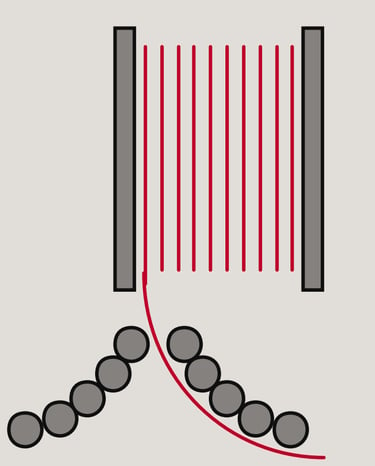
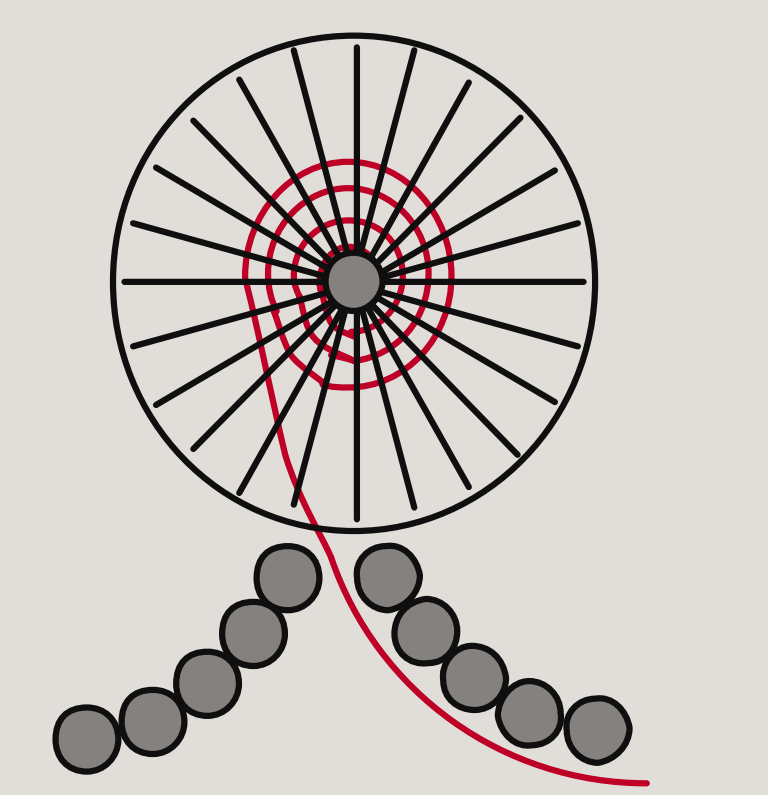
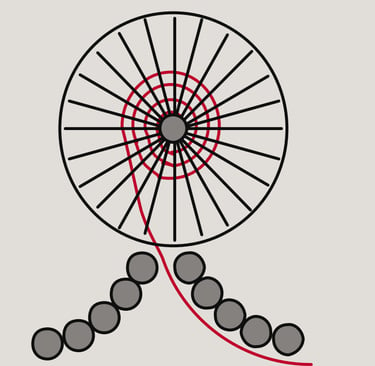
Reeling Cable Solutions
Expertise in flexible power cables for mobile machinery in port terminals and shipyards.
Flexible Power Cables
Designed for high mechanical stress and frequent bending in various material handling equipment.
Energy Supply Systems
Optimized for cable reels and trolley systems with strong acceleration and fast movements.
FeiChun Cable Reel Cables for Port Terminals
Our reel cables boast high durability and superior flexibility. They are specifically designed to resist corrosion from salt spray and aggressive sea winds, and they can easily fend off the damaging effects of oil and grease. This unique combination ensures smooth winding and unwinding, reducing downtime and maintaining optimal performance even in the most challenging marine environments.
Advanced Durability and Flexibility
Applications in Port Machinery
FeiChun Cable reel cables are the ideal choice for a wide range of port terminal machinery. They are widely used in container cranes, forklifts, winches, and hydraulic cable handling systems. Additionally, these cables perform reliably in electric hoists, automated guided vehicles, and other heavy-duty port equipment, ensuring safe and efficient cargo handling operations.
FeiChun Cable reel cables are engineered for port terminal applications, where durability and flexibility are key. Our cables are built to last, crafted from robust materials that withstand heavy usage and extreme conditions. They deliver exceptional performance even when exposed to the harsh elements of sea winds and oil contamination.
With a strong focus on quality and innovation, FeiChun Cable continues to set industry benchmarks by providing reel cables that combine exceptional durability with high flexibility, even under the relentless exposure to sea wind corrosion and oil contamination.
